Innovation
At Plastipack, we heavily invest in the Research and Development of our pool and water storage cover materials.
Innovation is written into the core values of the company, with our team focused on the constant improvement of our products and processes.
On Site Testing
GeoBubble™ materials are developed, manufactured and tested at Plastipack HQ, where we have a dedicated Research and Development team, supported by placement students from The University of Surrey. On site, we have a bespoke testing facility consisting of five identical swimming pools. This enables the team to conduct comparative testing of different cover materials, allowing us to test the effectiveness of any products in development, and to perform quality control on products already in the market.
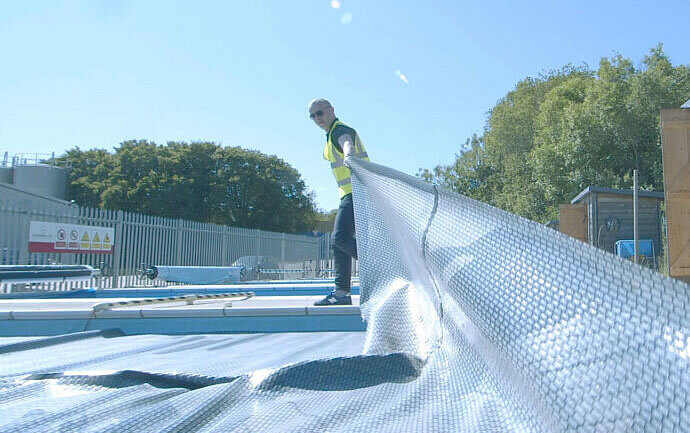
The pools at our testing facility are designed to be representative of an average sized, privately owned pool. Each pool is unheated, and measures 8m X 4m with a 1.3m depth and a volume of 41,600L. Each pool is serviced by its own 0.75hp filtration pump running for 8 hours each day (6 hours during the day, 2 at overnight), a pattern commonly accepted as industry best practice. In order to determine the benefits of covering an outdoor pool with our GeoBubble™ materials, test pools are covered with a selection of our GeoBubble™ covers, with one pool left uncovered to act as a control.
Details and results of all of these tests can be found in the Case studies on our Resources page.
Water temperature testing
Each pool contains an array of 6 type-T thermocouples at its centre, continually logging water temperature at incremental depths and calculating average water temperature.
Chemical consumption testing
During testing, water samples are taken every other day to ensure that chemical concentrations remained within the accepted industry standard. Any chemical additions required to restore and rebalance water chemistry to within the acceptable limits are recorded.
Evaporation testing
In order to determine the effects of GeoBubble™ products with respect to controlling evaporation from the surface of a pool, a test was devised using two unheated tanks positioned outdoors in direct sunlight. One was covered with a GeoBubble™ product, and the other was left uncovered. At the conclusion of the test, the water depths of both tanks were measured and used to calculate the water remaining in each tank. The percentage of water lost by evaporation was
subsequently calculated for comparison.
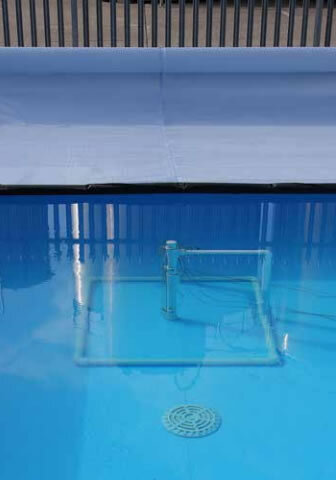
Lifespan testing
A domed bubble shape was created, 50% thicker than a traditional bubble at its thinnest point. Two bubbles were then joined together to increase the room for air expansion and create a strong structural arch to resist collapse. Accelerated weathering testing proved the development significantly improved the swimming pool bubble cover material’s lifespan – up to 25% longer than materials with the traditional bubble design.
Award winning team
In 2018, our R&D team were the proud recipient of the Business Innovation Award from the Institute of Physics. Awarded for the development of our groundbreaking EnergyGuard™ Selective Transmission pool cover material; this prize reflected the deeply entrenched science-based focus of the team and the company in the development of our product range.
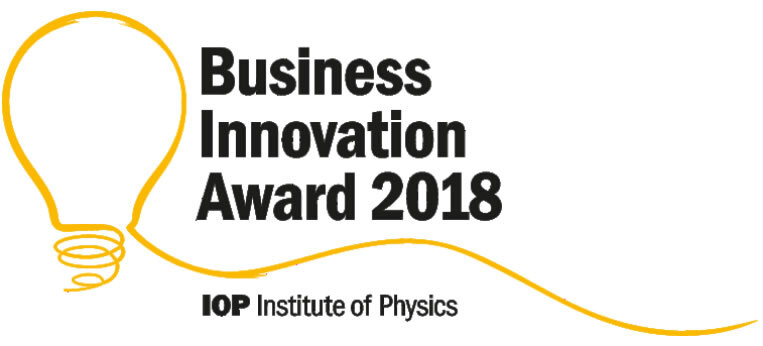
“This new product represents a disruptive innovation enabling the company to strategically position themselves as world leading in a highly competitive market awash with low cost manufacturers.”
Institute of Physics, 2018 Business Innovation Award.
Collaboration with Universities
As a forward-thinking business, we understand how increasing our knowledge base can impact the company’s growth. Since the very early days of Plastipack, we’ve worked closely with UK universities in the development of our product range and processes.
The birth of GeoBubble™ Technology
GeoBubble™ Technology was born through a collaboration between ourselves and the product design and material science departments of two UK universities.
The teams set out to remove the inherent weaknesses from the traditional swimming pool bubble cover design. After extensive research and testing, the GeoBubble™ shape was designed with a smooth uniform profile to compliment the polymer’s natural behaviour.
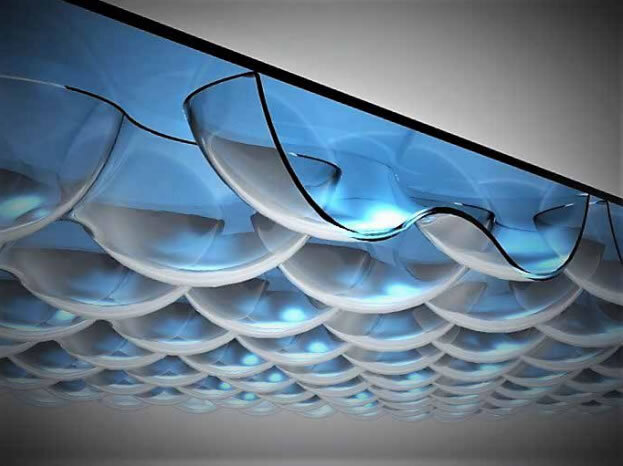
A domed bubble shape was created, 50% thicker than a traditional bubble at its thinnest point. Two bubbles were then joined together to increase the room for air expansion and create a strong structural arch to resist collapse. Accelerated weathering testing proved the development significantly improved the swimming pool bubble cover material’s lifespan – up to 25% longer than materials with the traditional bubble design.
After 5 years of development, GeoBubble™ technology was launched in 2012 and has since been sold around the world, providing the longest possible lifespan for the material and ensuring the pool cover continues to provide energy and resource savings throughout its useful life.
University Placement Programme
This collaborative working continues to this day. Each year we take on a placement student to work alongside the R&D department as part of their undergraduate or master’s degree. Students from disciplines such as Mechanical or Aerospace engineering, Physics and Maths have come to us for their year in the industry and gained valuable hands-on work experience in a growing industry. Many have been involved in significant improvements to our working processes as well as in the launch of new products.
Placement Highlights
Placement students have been involved in projects and achievements including:
Product launches:
- The award-winning EnergyGuard™ Selective Transmission pool cover material
- CoolGuard™ Ultra
- RaeGuard™ – named after the placement student, in part as thanks for their contribution to the project
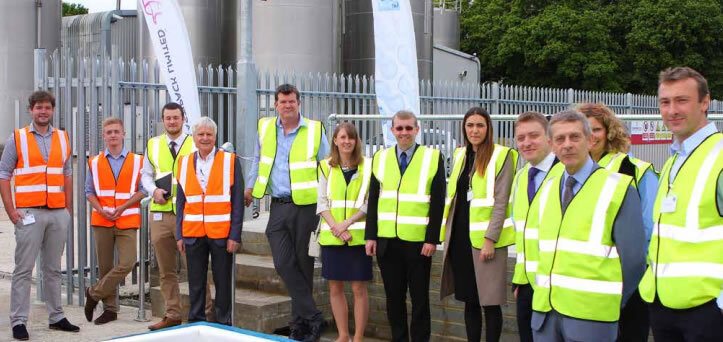
Awards and Achievements:
- Winner of Placement Award for Sustainability for 2022 from University of Surrey
- Speaking at the National Instruments conference about work he did for us
Process improvements:
- Opening of pool testing facility
- Creation of MatLab simulation
- Creation of LabView bespoke testing
- Improved recycling procedures in the factory, for which they won the Sustainability award mentioned above
- General machine and product flow improvements